Rittal Automation Day: Experten-Tipps gegen den Kostendruck
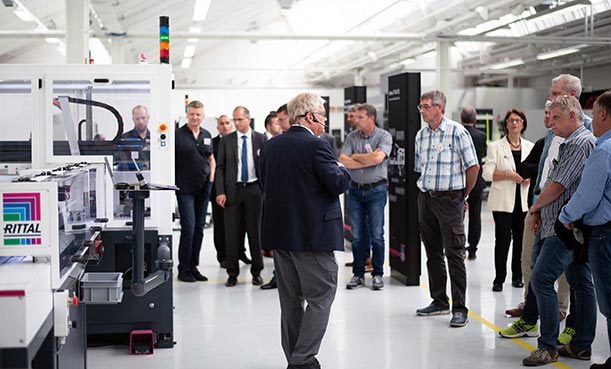
Die Teilnehmer informierten sich im Rittal Innovation Center über die neueste Automatisierungslösungen von Rittal und Eplan für den Steuerungs- und Schaltanlagenbau. Quelle Rittal GmbH & Co. KG
Die Anforderungen an den Steuerungs- und Schaltanlagenbau werden immer höher. Kosten- und Termindruck sind praktisch bei jedem Auftrag ein Thema, mit dem der Anlagenbauer konfrontiert wird. Wie diese Herausforderungen mit zunehmender Automatisierung zu bewältigen sind, diskutierten rund 50 Fachleute aus der Branche mit den Experten von Rittal auf dem 2. Rittal Automation Day am 24. Mai 2018 in Haiger.
„Die Auftragsbücher sind voll“ – Diese Aussage hätten wahrscheinlich alle Teilnehmer des Rittal Automation Day sofort unterschrieben. Die Frage, die viele Fachleute der Branche deswegen umtreibt, lautet: „Wie lassen sich die Prozesse im Engineering und in der Elektrowerkstatt optimieren, um dadurch die Produktivität zu erhöhen?“
Hoher Termin- und Kostendruck
„Die grundlegenden Anforderungen im Steuerungs- und Schaltanlagenbau sind bei den meisten Unternehmen ähnlich“, fasst Jan-Henry Schall, Leiter des Rittal Innovation Centers, die Erwartungen zusammen, die er zu Beginn der Veranstaltung bei den Teilnehmern abfragt: Hoher Kosten- und Termindruck, Fachkräftemangel und ineffiziente Abläufe in der Werkstatt wurden am häufigsten genannt. Manuell und häufig redundant ausgeführte manuelle Tätigkeiten sind oft eine Hauptquelle für diese Ineffizienz. So werden Daten sehr oft mehrfach erfasst etwa in der Planung, anschließend bei der kaufmännischen Abwicklung und noch einmal oder mehrmals in der Werkstatt. Solche Abläufe sind nicht nur ineffizient, sie können gleichzeitig leicht zu Fehlern und damit zu einem zusätzlichen Aufwand führen.
Virtuelles Prototyping als Erfolgsfaktor
Der Hauptansatzpunkt zur Optimierung der Abläufe im Steuerungs- und Schaltanlagenbau basiert auf dem Einsatz des „Virtuellen Prototypings“, bei dem im Engineering ein digitaler Zwilling des Schaltschranks erzeugt wird. Die Daten des „Virtuellen Prototyps“ lassen sich anschließend in der Werkstatt verwenden, um damit automatisierte Systeme anzusteuern. „Damit sind umfangreiche Prozessoptimierungen und -steigerungen möglich“, sagt Jan-Henry Schall. Gerade die mehrfache redundante Erfassung von Daten lasse sich so wirkungsvoll minimieren.
Automatisierung lohnt sich ab 100 Schränke
Welche Lösungen Rittal Automation Systems anbietet und welche Einsparungen sich damit erzielen lassen, erläuterte Tim Kramer, Director Product Management. Mit einem Perforex BC Bearbeitungszentrum, das Bohrungen, Gewinde und Ausbrüche in die Flachteile des Schaltschranks vollautomatisch einbringt, lässt sich zum Beispiel der manuelle Zeitaufwand für diese Schritte bei einem typischen Schaltschrank von über acht Stunden auf rund 30 Minuten reduzieren.
In vielen Unternehmen – gerade bei kleineren Mittelständlern – stellt sich die Frage, ob sich die Investitionen in solche automatisierte Lösungen rechnen. Jan-Henry Schall präsentierte hierzu Zahlen, die auf über 100 Kundenbefragungen basieren und durch eine Studie der Universität Stuttgart untermauert wurden.
Darin befindet sich eine detaillierte Analyse der Aufwände bei der Produktion eines typischen Schaltschranks in der Elektrowerkstatt. Die in der Studie bestimmten 58 Stunden Arbeitszeit pro Schaltschrank bei rein handwerklicher Ausführung sämtlicher Arbeiten lassen sich durch eine ganzheitliche Optimierung auf rund 34 Stunden senken – die Lohnkosten sinken von 2.200 € auf 1.300 €. Das für viele erstaunliche Ergebnis dieser Beispielrechnung: Auch wenn nur 100 Schaltschränke pro Jahr bearbeitet werden, amortisiert sich die Investition in ein Perforex-Bearbeitungszentrum BC innerhalb von zweieinhalb bis drei Jahren.
Viele andere Investitionen in automatisierte oder teilautomatisierte Lösungen amortisieren sich ebenfalls auch bei kleineren Steuerungs- und Schaltanlagenbauern sehr schnell. Das Spektrum reicht von der Kabelkonfektionierung über den automatisierten Zuschnitt von Tragschienen und Kabelkanälen bis zur Unterstützung bei der Verdrahtung. „Ziel aller Lösung ist es“, so Tim Kramer, „eine hohe Wirtschaftlichkeit auch bei kleinen Losgrößen zu realisieren.“
Durchgängige Datenhaltung
Die Basis für alle Schritte entlang der Wertschöpfungskette im Steuerungs- und Schaltanlagenbau wird im Engineering gelegt. Die Möglichkeiten, die die Software-Lösungen Eplan Electric P8 und Eplan Pro Panel bieten, zeigte Michael Kranz, Consultant Wertschöpfungskette bei Eplan. Besonders beeindruckend für die Teilnehmer war die nahtlose Integration zwischen Elektrokonstruktion, virtueller Aufbauplanung, dem Eplan Data Portal und den Konfiguratoren von Rittal. „In der Elektrokonstruktion haben wir alles – nur keine Zeit“, war die Kernaussage von Michael Kranz. Es gelte Prozesse zu optimieren, um mehr Zeit für das Engineering zu gewinnen.
Wie der gesamte Workflow in der Praxis optimiert werden kann, demonstrierte Oliver Martin von Bauer Systeme. Das mittelständische Unternehmen hat praktisch alle auf dem Automation Day vorgestellten Lösungen bereits implementiert. „Der Fokus liegt auf den Daten“, macht Oliver Martin deutlich: „Die Eplan-Datenbank ist der Schlüssel in unserem Engineering-Prozess und wird entsprechend sorgfältig gepflegt.“ Mit einem durchgängigen Engineering und den daraus generierten Daten lassen sich dann die Prozesse in der Werkstatt optimieren. Das Ergebnis ist eine hohe Effizienz bei gleichzeitig niedrigen Kosten.
Die rund 50 Teilnehmer des Rittal Automation Day zeigten sich mit der Veranstaltung hochzufrieden. „Sehr beeindruckend“ und „Wir haben viele neue Impulse erhalten“, lauteten die Kommentare.
Über Rittal
Rittal mit Sitz in Herborn, Hessen, ist ein weltweit führender Systemanbieter für Schaltschränke, Stromverteilung, Klimatisierung, IT-Infrastruktur sowie Software & Service. Systemlösungen von Rittal sind in über 90 Prozent aller Branchen weltweit zu finden, etwa im Maschinen- und Anlagenbau, der Nahrungs- und Genussmittelindustrie sowie in der IT- und Telekommunikationsbranche.
Zum breiten Leistungsspektrum des Weltmarktführers gehören konfigurierbare Schaltschränke, deren Daten im gesamten Produktionsprozess durchgängig verfügbar sind. Intelligente Rittal Kühllösungen mit bis zu 75 Prozent geringerem Energie- und CO2-Verbrauch können mit der Produktionslandschaft kommunizieren und ermöglichen vorausschauende Wartungs- und Servicekonzepte. Innovative IT-Lösungen vom IT-Rack über das modulare Rechenzentrum bis hin zu Edge und Hyperscale Computing Lösungen gehören zum Portfolio.
Die führenden Softwareanbieter Eplan und Cideon ergänzen die Wertschöpfungskette durch disziplinübergreifende Engineering-Lösungen, Rittal Automation Systems durch Automatisierungslösungen für den Schaltanlagenbau. Rittal liefert in Deutschland binnen 24 Stunden zum Bedarfstermin – punktgenau, flexibel und effizient.
Rittal wurde im Jahr 1961 gegründet und ist das größte Unternehmen der inhabergeführten Friedhelm Loh Group. Die Friedhelm Loh Group ist mit 18 Produktionsstätten und 80 Tochtergesellschaften international erfolgreich. Die Unternehmensgruppe beschäftigt 11.500 Mitarbeiter und erzielte im Jahr 2017 einen Umsatz von 2,5 Milliarden Euro. Zum zehnten Mal in Folge wurde das Familienunternehmen 2018 als Top Arbeitgeber Deutschland ausgezeichnet. In einer bundesweiten Studie stellten die Zeitschrift Focus Money und die Stiftung Deutschland Test fest, dass die Friedhelm Loh Group 2018 bereits zum dritten Mal in Folge zu den bundesweit besten Ausbildungsbetrieben gehört.
Weitere Informationen finden Sie unter www.rittal.de und www.friedhelm-loh-group.com
Unternehmenskommunikation
Regina Wiechens-Schwake
Tel.: 02772/505-2527
E-Mail: wiechens-schwake.r@rittal.de
Hans-Robert Koch
Tel.: 02772/505-2693
E-Mail: koch.hr@rittal.de
Christian Abels
Tel.: 02772/505-1328
E-Mail: abels.c@rittal.de
Rittal GmbH & Co. KG
Auf dem Stützelberg
35745 Herborn
Media Contact
Alle Nachrichten aus der Kategorie: Unternehmensmeldungen
Neueste Beiträge

Spitzenforschung in der Bioprozesstechnik
Das IMC Krems University of Applied Sciences (IMC Krems) hat sich im Bereich Bioprocess Engineering (Bioprozess- oder Prozesstechnik) als Institution mit herausragender Expertise im Bereich Fermentationstechnologie etabliert. Unter der Leitung…

Datensammler am Meeresgrund
Neuer Messknoten vor Boknis Eck wurde heute installiert. In der Eckernförder Bucht, knapp zwei Kilometer vor der Küste, befindet sich eine der ältesten marinen Zeitserienstationen weltweit: Boknis Eck. Seit 1957…

Rotorblätter für Mega-Windkraftanlagen optimiert
Ein internationales Forschungsteam an der Fachhochschule (FH) Kiel hat die aerodynamischen Profile von Rotorblättern von Mega-Windkraftanlagen optimiert. Hierfür analysierte das Team den Übergangsbereich von Rotorblättern direkt an der Rotornabe, der…