Drucksensor aus Silizium-Carbid misst bei 600° C
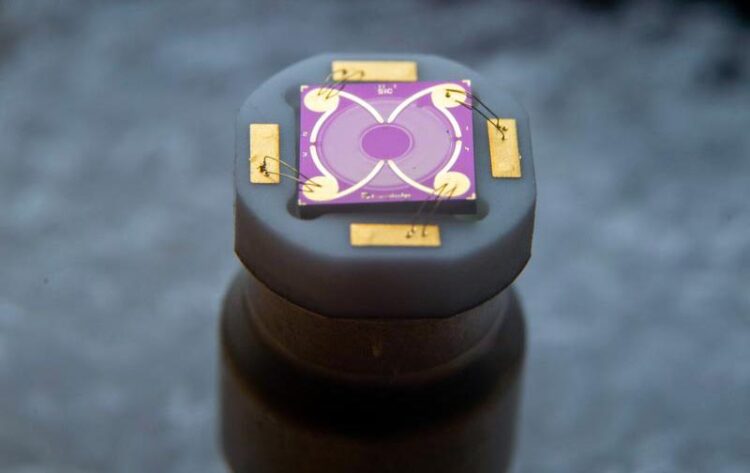
Ein spezieller Ätzprozess ermöglicht Sensoren für Einsatztemperaturen bis 600° C.
Bild: Fraunhofer IZM
… und könnte das Fliegen umweltverträglicher machen.
Er misst dort, wo es richtig heiß wird: Während übliche Sensoren bei einer Umgebungstemperatur von 300° C den elektronischen Geist aufgeben, entwickeln Forschende des Fraunhofer IZM einen zuverlässigen Sensor, der auch bei doppelt so hohen Temperaturen sicher arbeitet. Mittels präziser Ätzvorgänge machten sie Silizium-Carbid für den Aufbau eines robusten Sensors nutzbar. Durch die Druckmessungen in extrem rauen Umgebungen könnten beispielsweise Verbrennungsprozesse in Flugzeugturbinen kontrolliert und damit der Kerosinverbrauch reduziert werden.
Der Traum vom Fliegen begleitet die Menschheit schon Jahrtausende lang: Vom griechischen Ikarus-Mythos bis hin zu den Überlegungen Da Vincis wurde die Phantasie schrittweise mit technischem Wissen angereichert. Seit der Entwicklung der Turbinen-Stahltriebwerke Mitte des 20. Jahrhunderts sind Objekte mit hoher Leistung und Schubkraft in der Luft. Die Funktionsweise: Mittels einer Gasturbine und der Rückstoßwirkung des Luft- sowie Abgasstroms wird hohe Schubkraft erzeugt und der Flugkörper angetrieben. Was von außen nicht sichtbar ist: Durch die starke Kompression der angesogenen Luft herrscht in der Flugzeugturbine enormer Druck und die Temperaturen steigen schon beim Eintritt in die Brennkammer auf bis zu 600° C. Bei Raumfahrtapplikationen ist die Umgebung noch rauer. Um Sicherheit in der Luft- und Raumfahrt zu gewährleisten und die Verhältnisse während der Nutzung kontrollieren zu können, werden Sensoren eingesetzt. Diese müssen jedoch speziellen Anforderungen entsprechen: Zusätzlich zur Genauigkeit und Sensibilität müssen sie zuverlässig sein und den extrem korrosiven Umgebungsbedingungen standhalten.
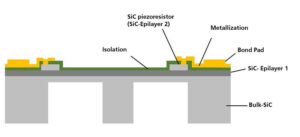
Mit dem Tiefenätzen konnte der Aufbau temperaturbeständig sowie biegbar realisiert werden.
Bild: Fraunhofer IZM
Forschende des Fraunhofer IZM im Norden Berlins haben es sich zur Aufgabe gemacht, einen Hochtemperatur-Sensor zu entwickeln und aufzubauen, der diesen Anforderungen entspricht: Dafür nutzen sie Silizium-Carbid (SiC). Das Material stellt für den Aufbau von Drucksensoren vor allem hinsichtlich der Robustheit einen technologischen Durchbruch dar. Die Nutzung klassischer Silizium-Sensoren ist für Anwendungen dieser Art unvorstellbar, denn diese geraten schon bei 150° C an ihre Belastungsgrenze. Sensoren, die auf der sogenannten SOI-Technologie (Silicon on Insulator) basieren, schneiden besser ab, jedoch beginnt auch hier bei Temperaturen über 400° C in Kombination mit mechanischer Belastung eine plastische Deformation, was die Messgenauigkeit ungünstig beeinflusst.
Die neue Generation der Hochtemperatur-Sensoren auf SiC aufzubauen, bietet klare Vorteile: Das Material ist extrem robust, thermisch stabil und reagiert kaum auf chemische Einflüsse. Zudem erlaubt die hohe Bandbreite des Materials eine Nutzung bei Temperaturen bis zu 600° C. Bei diesen mechanischen und chemischen Voraussetzungen, wurde es schon vor Jahren als mögliches „Wundermaterial“ in der Mikroelektronik erkannt. Die bis dahin bestehende Herausforderung lag besonders in der Bearbeitung des Materials: „Silizium-Carbid ist Fluch und Segen zugleich: Die einzigartige Festigkeit und Beständigkeit des Materials sind vielversprechend für elektronische Komponenten. Genau diese Eigenschaften machen es aber auch extrem schwierig, das SiC zu bearbeiten.“, so Wissenschaftler Piotr Mackowiak vom Fraunhofer IZM.
Hierfür hat die Forschungsgruppe um Mackowiak nun Lösungsansätze gefunden. Ihre Herausforderung bestand darin, in einem Halbleiterprozess einen winzigen stabilen Grundkörper auf einer dünnen Membran aufzubauen. Dafür verwendeten sie einen zweifachen, äußerst schnellen Ätzprozess. Dieser ätzt das Siliziumcarbid mit einer Geschwindigkeit von 4 Mikrometern pro Minute auf, was dem 8-fachen der gängigen Raten entspricht und damit für hochvolumige Fertigungsdurchsätze interessant ist. Das Endprodukt der Fertigung zeichnet sich zudem durch eine außergewöhnliche Geometrie aus, die zur Temperaturbeständigkeit beiträgt und ermöglicht, dass keine externe Kühlung des Sensors notwendig ist.
„Ziel war es, den Aufbau einerseits nur auf das Notwendigste zu beschränken, so dass die Temperaturbeständigkeit sichergestellt wird, andererseits das Material stellenweise so abzudünnen, dass es biegbar wird, um Piezomessungen zu ermöglichen – beides ist uns mit dem Tiefenätzen gelungen“, so Mackowiak. Bereits existierende Sensoren in diesem Bereich arbeiten nach dem piezoelektrischen Messprinzip. Dies hat den Nachteil, dass nur dynamische und keine statischen Drücke erfasst werden können. Auch können die existierenden Sensoren sehr hohe Temperaturen nicht dauerhaft aushalten. „Unsere Sensoren arbeiten piezoresisitiv. Dies erlaubt das Messen von dynamischem und statischem Druck. Unsere Sensoren können dauerhaft und bei noch höheren Temperaturen betrieben werden.“ Zukünftige Projektpartner können nun den Sensor und das Package erwerben oder sich an der Weiterentwicklung des Sensors mit veränderten Parametern beteiligen.
Zuverlässige Hochtemperaturmessungen bis zu 600° C könnten zu mehr Umweltverträglichkeit in der Luftfahrt beitragen. Auf der Basis der Messungen der thermoakustischen Druckschwingungen und Prozessparameter in der Turbine wird eine deutlich höhere Prozesskontrolle erzielt: Das Verhältnis des Luft-Brennstoff-Gemischs könnte angepasst und die Verbrennung optimiert werden. Dies würde zu einer Reduktion des Kerosinverbrauchs führen.
Durch kleine Änderungen des Designs können die Messgrößen variiert werden, wodurch der Sensor nicht nur für die Luft- und Raumfahrt, sondern perspektivisch auch im Bereich der E-Mobilität oder für Messungen bei Tiefenbohrungen einsetzbar wird.
(Text: Olga Putsykina)
Wissenschaftliche Ansprechpartner:
Piotr Mackowiak l Telefon +49 30 46403-7981 l Piotr.Mackowiak@izm.fraunhofer.de | Fraunhofer-Institut für Zuverlässigkeit und Mikrointegration IZM I Gustav-Meyer-Allee 25 | 13355 Berlin | www.izm.fraunhofer.de |
Originalpublikation:
https://www.izm.fraunhofer.de/de/de/news_events/tech_news/drucksensor-koennte-da…
Media Contact
Alle Nachrichten aus der Kategorie: Energie und Elektrotechnik
Dieser Fachbereich umfasst die Erzeugung, Übertragung und Umformung von Energie, die Effizienz von Energieerzeugung, Energieumwandlung, Energietransport und letztlich die Energienutzung.
Der innovations-report bietet Ihnen hierzu interessante Berichte und Artikel, unter anderem zu den Teilbereichen: Windenergie, Brennstoffzellen, Sonnenenergie, Erdwärme, Erdöl, Gas, Atomtechnik, Alternative Energie, Energieeinsparung, Fusionstechnologie, Wasserstofftechnik und Supraleittechnik.
Neueste Beiträge

Größte bisher bekannte magnetische Anisotropie eines Moleküls gemessen
An der Berliner Synchrotronstrahlungsquelle BESSY II ist es gelungen, die größte magnetische Anisotropie eines einzelnen Moleküls zu bestimmen, die jemals experimentell gemessen wurde. Je größer diese Anisotropie ist, desto besser…

Tsunami-Frühwarnsystem im Indischen Ozean
20 Jahre nach der Tsunami-Katastrophe… Dank des unter Federführung des GFZ von 2005 bis 2008 entwickelten Frühwarnsystems GITEWS ist heute nicht nur der Indische Ozean besser auf solche Naturgefahren vorbereitet….

Resistente Bakterien in der Ostsee
Greifswalder Publikation in npj Clean Water. Ein Forschungsteam des Helmholtz-Instituts für One Health (HIOH) hat die Verbreitung und Eigenschaften von antibiotikaresistenten Bakterien in der Ostsee untersucht. Die Ergebnisse ihrer Arbeit…