Textilherstellung für Weltraumantennen startet in die Industrialisierungsphase
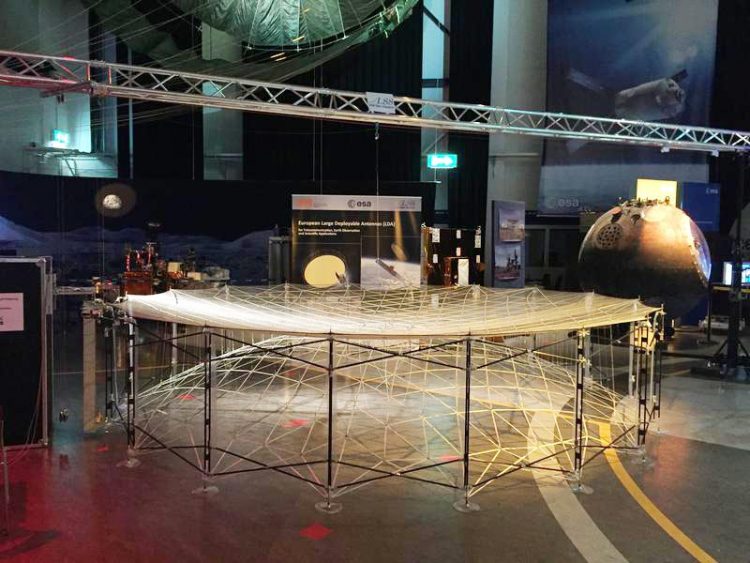
Reflektorantenne als 5 m Ingenieursmodell Foto: ESA, HPS GmbH, LSS GmbH
Beim Stichwort Raumfahrt werden zunächst Assoziationen zu Forschungen auf Mond und Mars sowie zur Beobachtung ferner Galaxien geweckt. Für unseren Alltag sind jedoch besonders die Anwendungen der Raumfahrt im erdnahen Raum relevant.
Mittels erdbeobachtender Satelliten können beispielsweise Klimaveränderungen nachvollzogen oder Wettervorhersagen gemacht werden.
Auch die moderne Telekommunikations- und Navigationstechnik wird unterstützt von Satelliten im Erdorbit. In der globalen Wirtschaft sind schnelle Datenübertragungen unverzichtbar.
Die zur Erdbeobachtung und Telekommunikation verwendeten Satellitenantennen haben einen parabolischen Reflektor, der die elektromagnetische Strahlung bündelt.
Der Durchmesser dieses Reflektors wird bestimmt von den jeweiligen Missionsanforderungen, wie z. B. der benötigten Bildauflösung oder der zu übertragenden Datenmenge.
Sehr große Reflektoren mit Durchmessern von 5 m bis 20 m spielen eine zunehmend wichtige Rolle; gleichzeitig sollen jedoch Gewicht und Packmaß der Antennen für einen ökonomischen Transport ins All gering gehalten werden.
Textile Materialien für die reflektierende Oberfläche können diesen Anforderungen gerecht werden. Sie ermöglichen die Herstellung leichter, faltbarer Strukturen in nahezu beliebiger Form und Größe.
Die Entwicklung von faltbaren Weltraumantennen hat in Europa gerade erst begonnen. Die Herausforderungen für solche Antennen liegen u. a. in der Fertigung der hochpräzisen, hochreflektierenden Oberfläche aus ultrafeinem Metallgewirk, welches gleichzeitig eine hohe elastische Dehnung ermöglichen muss.
Außerdem werden sehr hohe Anforderungen an die Drapierfähigkeit, ein kleines Packmaß und die elektrische Leitfähigkeit der technischen Textilien gestellt. Weltweit können derartige Antennen lediglich in den USA hergestellt werden. Um eine größere europäische Unabhängigkeit bei Weltraummissionen zu erreichen, wird die Entwicklung der Technologie von der europäischen Raumfahrtagentur ESA sowie der europäischen Kommission unterstützt.
Im EU-Projekt LEA (Large European Antenna) arbeiten mehr als 15 europäische Unternehmen und Forschungseinrichtungen an der Entwicklung der Antennenkomponenten. Aus Deutschland sind u. a. die HPS GmbH beteiligt, ein Raumfahrtunternehmen aus München, welches als Hauptauftragnehmer agiert, sowie – aus Münchberg – die Iprotex GmbH & Co. KG, welche auf technische Textilien spezialisiert ist, und das Fraunhofer-Anwendungszentrum für Textile Faserkeramiken TFK.
Sie fokussieren sich auf die Entwicklung der textilen Oberfläche des Reflektors. „Wir sind stolz, dass wir mit unserer Expertise zum Gelingen des Projekts beitragen können. Erste Prototypen wurden am Campus der Hochschule Hof in Münchberg sogar schon hergestellt und an das Raumfahrtunternehmen HPS geliefert“, so Prof. Dr. Frank Ficker, Leiter des Fraunhofer- Anwendungszentrums TFK.
Durch das neu gegründete Unternehmen HPTex, hervorgegangen in gleichen Anteilen aus den Unternehmen HPS und Iprotex, soll die Textilherstellung für Reflektorantennen nun in einer Industrialisierungsphase auf eine neue Ebene gehoben werden. Eines der Hauptziele ist die Herstellung extrem feiner Metallgewirke für die Übertragung von Frequenzen im Ka-Band Bereich für Reflektordurchmesser bis zu 8 m.
„Mit der Neugründung haben wir die Kompetenzen von HPS im Bereich Raumfahrtantennen sowie die von Iprotex in der Herstellung technischer Gewirke gebündelt. Dass das Fraunhofer-Anwendungszentrum für Textile Faserkeramiken TFK auch zukünftig mit uns die Forschung und Entwicklung weiter vorantreiben wird, stellt für unser Unternehmen einen entscheidenden Erfolgsfaktor dar“, so Peter Rauhut, Geschäftsführer von HPTex.
Bis Ende 2020 soll die erste 5 m Reflektorantenne LEA-X5 fertig gestellt und unter Weltraumbedingungen getestet werden. Das reflektierende Metallnetz dafür wurde bereits im vergangenen Jahr geliefert. Zurzeit ist eine zweite Reflektorantenne LEA-K8r mit 8 m Durchmesser im Bau; die Testkampagne ist für das erste Quartal 2021 geplant. Das funktionale Kernstück dieser Antenne, das Metallnetz, wird im August 2020 hergestellt.
Das Fraunhofer-Anwendungszentrum für Textile Faserkeramiken TFK in Münchberg ist spezialisiert auf die Entwicklung, Herstellung und Prüfung textiler keramischer Komponenten. Es gehört zum Fraunhofer-Zentrum für Hochtemperatur-Leichtbau HTL in Bayreuth, eine Einrichtung des Fraunhofer-Instituts für Silicatforschung ISC mit Hauptsitz in Würzburg.
Kontakt
Susanne Kuballa
Fraunhofer-Zentrum für Hochtemperatur-Leichtbau HTL
Gottlieb-Keim-Straße 62
95448 Bayreuth
Telefon +49 921 78510-940
susanne.kuballa@isc.fraunhofer.de
https://www.htl.fraunhofer.de/ Mehr zum Fraunhofer-Zentrum für Hochtemperatur-Leichtbau HTL
Media Contact
Alle Nachrichten aus der Kategorie: Informationstechnologie
Neuerungen und Entwicklungen auf den Gebieten der Informations- und Datenverarbeitung sowie der dafür benötigten Hardware finden Sie hier zusammengefasst.
Unter anderem erhalten Sie Informationen aus den Teilbereichen: IT-Dienstleistungen, IT-Architektur, IT-Management und Telekommunikation.
Neueste Beiträge

Lange angestrebte Messung des exotischen Betazerfalls in Thallium
… hilft bei Zeitskalenbestimmung der Sonnenentstehung. Wie lange hat eigentlich die Bildung unserer Sonne in ihrer stellaren Kinderstube gedauert? Eine internationale Kollaboration von Wissenschaftler*innen ist einer Antwort nun nähergekommen. Ihnen…

Soft Robotics: Keramik mit Feingefühl
Roboter, die Berührungen spüren und Temperaturunterschiede wahrnehmen? Ein unerwartetes Material macht das möglich. Im Empa-Labor für Hochleistungskeramik entwickeln Forschende weiche und intelligente Sensormaterialien auf der Basis von Keramik-Partikeln. Beim Wort…

Klimawandel bedroht wichtige Planktongruppen im Meer
Erwärmung und Versauerung der Ozeane stören die marinen Ökosysteme. Planktische Foraminiferen sind winzige Meeresorganismen und von zentraler Bedeutung für den Kohlenstoffkreislauf der Ozeane. Eine aktuelle Studie des Forschungszentrums CEREGE in…