EHLA 3D: Eroberung der dritten Dimension
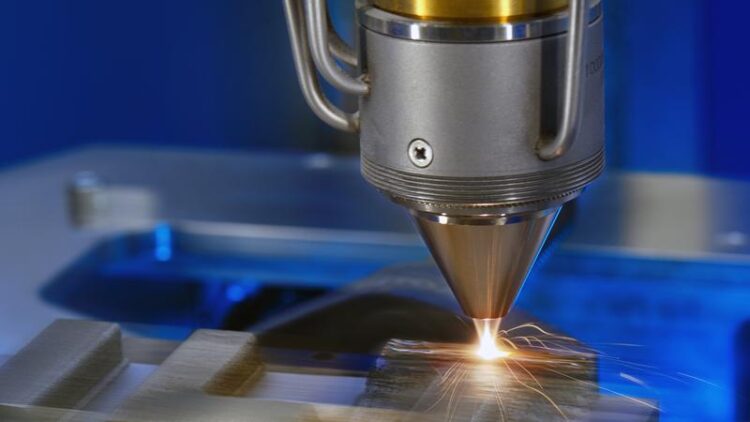
3D-Druck eines Fraunhofer ILT-Schriftzuges aus drei verschiedenen Pulverwerkstoffen als Demonstrator-Bauteil für das neue, hochproduktive EHLA-3D-Verfahren.
© Fraunhofer ILT, Aachen
Das am Fraunhofer-Institut für Lasertechnik ILT entwickelte Extreme Hochgeschwindigkeits-Laserauftragschweißen EHLA gilt als effiziente und umweltfreundliche Alternative zu den herkömmlichen Beschichtungsverfahren. Wesentliche Vorteile bringt es vor allem dort, wo metallische Bauteile extrem beansprucht und deshalb durch Beschichtung vor Korrosion und Verschleiß geschützt werden sollen. Zusammen mit der Ponticon GmbH arbeiten Wissenschaftlerinnen und Wissenschaftler des Fraunhofer ILT unter der Bezeichnung EHLA 3D nun daran, das patentierte Verfahren für die additive Fertigung weiterzuentwickeln und damit die Möglichkeiten des Verfahrens um ein Vielfaches zu erweitern.
Metallische Bauteile sind häufig extremen Bedingungen ausgesetzt. Zum Beispiel beim Einsatz in der Luft- und Raumfahrt, auf Ölbohrplattformen im Meer, in Form von Papierwalzen, Hydraulikzylindern oder als Bremsscheiben in Autos. Spezielle Beschichtungen sollen die Werkstoffe deshalb vor Korrosion und schnellem Verschleiß bewahren. Mit dem technologischen Fortschritt jedoch steigen die Anforderungen auf dem internationalen Markt stetig. Die Nachfrage ist infolgedessen zunehmend gekennzeichnet vom Bedarf nach noch schnelleren Produktionszeiten, individuellen und hoch performanten Bauteilen sowie einem enorm hohen Preisdruck.
Keines der herkömmlichen Verfahren jedoch genügt diesen Standards noch. Sie sind weder ausreichend flexibel, ressourceneffizient noch wirtschaftlich genug, um schmelzmetallurgisch angebundene, dünne Schichten mit hoher Qualität auf Bauteil-Oberflächen aufzutragen. Das Hartverchromen, bis vor nicht allzu langer Zeit das gängigste Verfahren, wird von der EU seit September 2017 nur noch unter strengen Auflagen zugelassen. Denn die elektrochemische Abscheidung von giftigem Chrom (VI) schädigt die Umwelt nachhaltig.
Um diese Lücke zu schließen, haben Wissenschaftlerinnen und Wissenschaftler des Fraunhofer ILT deshalb ein alternatives Beschichtungsverfahren entwickelt: das Extreme Hochgeschwindigkeits-Laserauftragschweißen EHLA. Seit 2015 kommt es insbesondere für Beschichtungen zum industriellen Einsatz, jetzt erfolgt für EHLA der Schritt in die dritte Dimension.
Die perfekte Grundlage
EHLA punktet im Vergleich zu den herkömmlichen Verfahren in mehrfacher Hinsicht. Nicht umsonst gewannen Wissenschaftler des Fraunhofer ILT dafür 2017 den renommierten Joseph-von-Fraunhofer-Preis. Das von ihnen entwickelte Verfahren verbessert die Vorschubgeschwindigkeit, mit der die Oberfläche bearbeitet wird, im Vergleich zum klassischen Laserauftragschweißen von 0,5 bis 2 Meter pro Minute auf 50 bis 500 Meter pro Minute. Ein Bauteil lässt sich heute also 100- bis 250-mal schneller beschichten. Auch ist es möglich, wesentlich dünnere Schichten aufzutragen. Waren durch konventionelles Laserauftragschweißen Schichten von mindestens 500 Mikrometer Stand der Technik, sind jetzt minimal 25 Mikrometer möglich.
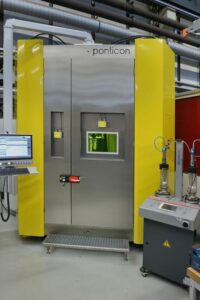
© Fraunhofer ILT, Aachen
Ein weiterer Vorteil liegt im geringen Wärmeeintrag. Beim klassischen Laserauftrag-schweißen wird der pulverförmige Zusatzwerkstoff in einem verhältnismäßig großen Schmelzbad direkt auf der Bauteiloberfläche aufgeschmolzen, um sie zu beschichten. Das kann die Materialeigenschaften jedoch nachhaltig verändern und kostet eine Menge Energie. Nicht so bei EHLA. Hier werden die festen Pulverpartikel schon in der Luft vom Laser aufgeschmolzen. Sie erreichen die Bauteiloberfläche also bereits im flüssigen Zustand und müssen dort nicht unter hohem Energieaufwand weiter aufgeschmolzen werden. Die Wärmeeinflusszone verkleinert sich so auf fünf bis zehn Mikrometer, beträgt also im Vergleich zum Laserauftragschweißen lediglich noch ein Hundertstel.
So können jetzt auch metallurgisch inkompatible, hitzeempfindliche Werkstoffgruppen miteinander verbunden und verarbeitet werden, Aluminium und Titan zum Beispiel. Insgesamt wird die Bauteil-Oberfläche zudem wesentlich glatter: die Rauheit verringert sich etwa um den Faktor 10. Für die Expertinnen und Experten am Fraunhofer ILT bietet das eine perfekte Grundlage für weitere Entwicklungsschritte.
Neue Generation der additiven Fertigung
»EHLA eignet sich im Prinzip für alles, was rotationssymmetrisch ist und auf einer schnellen Drehkinematik bearbeitet werden kann«, sagt Jonathan Schaible, wissenschaftlicher Mitarbeiter am Fraunhofer ILT. »Die Frage ist nur: Warum sollten wir uns auf einfache runde Teile beschränken, wenn eine weitaus größere Bandbreite an Einsatzmöglichkeiten denkbar ist?«
Aus diesem Grund arbeitet ein Team von Wissenschaftlern seit 2017 daran, eine neue Generation des Verfahrens zu entwickeln. Ihr Vorhaben: Die innovative Technologie für den 3D-Druck zu nutzen. Arbeitstitel: EHLA 3D. Schaibles Promotion darüber dürfte spannende Erkenntnisse zutage fördern. »Im Zentrum steht die Frage, welche speziellen Anforderungen für Maschinen- und Systemtechnik zu erfüllen sind, um EHLA mit dem Highspeed-3D-Druck kombinieren zu können.«
EHLA 3D ermöglicht gleich mehrere einzigartige, verfahrenstechnische Vorteile: hohe Aufbauraten, große Flexibilität und Materialvielfalt und gleichzeitig eine hohe Präzision. »In naher Zukunft sollen selbst komplexe, filigrane Strukturen im großen Maßstab einfach und kostengünstig hergestellt werden können«, sagt Schaible. »Auch individualisierte Bauteile sind denkbar.«
Erste Projekte gestartet
Der erste Prototyp der Anlage ist bereits erfolgreich im Einsatz. Er wurde 2019 in Zusammenarbeit mit der Ponticon GmbH aus Wiesbaden fertiggestellt. Das Konzept dafür basiert auf dem kinematischen Prinzip des Tripoden, einer Konstruktion mit drei Linearmotoren, die über Koppelstangen mit der Bauplattform, auf der das zu bearbeitende Bauteil bewegt wird, verbunden sind. »Das funktioniert ähnlich wie bei der Transrapid-Schwebebahn«, erklärt Schaible. »Der spezielle Aufbau gleicht die Trägheitskräfte weitgehend aus. In unserem Fall kann die Bauplattform dadurch sehr schnelle und präzise Bewegungen ausführen, ohne dass dabei große Schwingungen auftreten.« Inzwischen kann die Anlage so bis zu 25 Kilogramm schwere Bauteile bearbeiten – mit bis zu fünffacher Erdbeschleunigung und Geschwindigkeiten von bis zu 200 Metern pro Minute, bei zugleich sehr hoher Präzision von 100 Mikrometern. Beim herkömmlichen Laserauftragschweißen sind gerade einmal 0,5 bis 2 Meter pro Minute üblich.
»Um die Vorteile von EHLA 3D für einen großen Anwenderkreis im industriellen Umfeld nutzbar zu machen, werden am Fraunhofer ILT derzeit zielgerichtete Forschungsarbeiten durchgeführt«, sagt Schaible. »Auf dem Weg dorthin müssen wir die Komplexität beherrschbar machen.« Zentral sind etwa Prozessüberwachungskonzepte und automatisierte Bahnplanungs-Tools, am wichtigsten bleibt zunächst die Parametervariation im Labor. Bei der Prozessentwicklung müssen alle Parameter exakt aufeinander abgestimmt werden: Geschwindigkeit, Laserleistung und Pulvermenge in Abhängigkeit von der jeweils verarbeiteten Werkstoff-Kombination. »Da gibt es noch eine Menge experimenteller und empirischer Vorarbeit zu leisten. Die ersten Interessenten aus der Industrie haben aber schon ihre Fühler ausgestreckt«, ist Schaible optimistisch. »Wir sind also genau auf dem richtigen Weg.«
Derzeit wird EHLA 3D bereits in einem Projekt des Industriekonsortiums ICTM International Center for Turbomachinery Manufacturing unter Beteiligung zahlreicher namhafter Unternehmen aus den Bereichen Luftfahrt und Turbomaschinenbau weiter erforscht, ein Folgeprojekt ist für 2022 beantragt. Weitere bilaterale sowie öffentlich geförderte Konsortialprojekte und Machbarkeitsstudien sind in Planung. Die Bandbreite der Möglichkeiten für die Fertigung und Verarbeitung von Bauteilen wird mit EHLA 3D um ein Vielfaches erweitert, gleichzeitig effizienter und umweltverträglicher.
Fraunhofer ILT auf der Formnext 2021
Die Formnext findet vom 16. bis 19. November 2021 in Frankfurt am Main statt. Besuchen Sie unsere Expertinnen und Experten am Fraunhofer-Gemeinschaftsstand, Halle 12, Stand D41.
Vorträge zu diesem Thema
Erfahren Sie mehr auf der Onlinekonferenz ICAM 2021 – International Conference on Additive Manufacturing (ASTM International) vom 1.-5. November 2021 im Vortrag von Jonathan Schaible »Extreme High-Speed Laser Material Deposition for Additive Manufacturing«. Weitere Informationen: www.amcoe.org/icam2021
Auf dem AKL‘22 – International Laser Technology Congress, vom 4.-6. Mai 2022 in Aachen hält zudem Min-Uh Ko, Gruppenleiter Systemtechnik am Fraunhofer ILT, einen Vortrag zum Thema »Extreme High-Speed Laser Material Deposition for Additive Manufacturing«.
Weitere Informationen: www.lasercongress.org
Wissenschaftliche Ansprechpartner:
Dr.-Ing. Thomas Schopphoven
Kompetenzfeldleiter Laserauftragschweißen
Telefon +49 241 8906-8107
thomas.schopphoven@ilt.fraunhofer.de
Jonathan Schaible M.Sc.
Gruppe Systemtechnik LMD
Telefon +49 241 8906-660
jonathan.schaible@ilt.fraunhofer.de
Min-Uh Ko M.Sc.
Gruppenleiter Systemtechnik LMD
Telefon+49 241 8906-8441
min-uh.ko@ilt.fraunhofer.de
Weitere Informationen:
https://www.ilt.fraunhofer.de/
https://lia.scitation.org/doi/10.2351/7.0000320
https://ponticon.de/
Media Contact
Alle Nachrichten aus der Kategorie: Maschinenbau
Der Maschinenbau ist einer der führenden Industriezweige Deutschlands. Im Maschinenbau haben sich inzwischen eigenständige Studiengänge wie Produktion und Logistik, Verfahrenstechnik, Fahrzeugtechnik, Fertigungstechnik, Luft- und Raumfahrttechnik und andere etabliert.
Der innovations-report bietet Ihnen interessante Berichte und Artikel, unter anderem zu den Teilbereichen: Automatisierungstechnik, Bewegungstechnik, Antriebstechnik, Energietechnik, Fördertechnik, Kunststofftechnik, Leichtbau, Lagertechnik, Messtechnik, Werkzeugmaschinen, Regelungs- und Steuertechnik.
Neueste Beiträge

Größte bisher bekannte magnetische Anisotropie eines Moleküls gemessen
An der Berliner Synchrotronstrahlungsquelle BESSY II ist es gelungen, die größte magnetische Anisotropie eines einzelnen Moleküls zu bestimmen, die jemals experimentell gemessen wurde. Je größer diese Anisotropie ist, desto besser…

Tsunami-Frühwarnsystem im Indischen Ozean
20 Jahre nach der Tsunami-Katastrophe… Dank des unter Federführung des GFZ von 2005 bis 2008 entwickelten Frühwarnsystems GITEWS ist heute nicht nur der Indische Ozean besser auf solche Naturgefahren vorbereitet….

Resistente Bakterien in der Ostsee
Greifswalder Publikation in npj Clean Water. Ein Forschungsteam des Helmholtz-Instituts für One Health (HIOH) hat die Verbreitung und Eigenschaften von antibiotikaresistenten Bakterien in der Ostsee untersucht. Die Ergebnisse ihrer Arbeit…