3D trifft FVK: Mehr Flexibilität für hochbelastete Bauteile
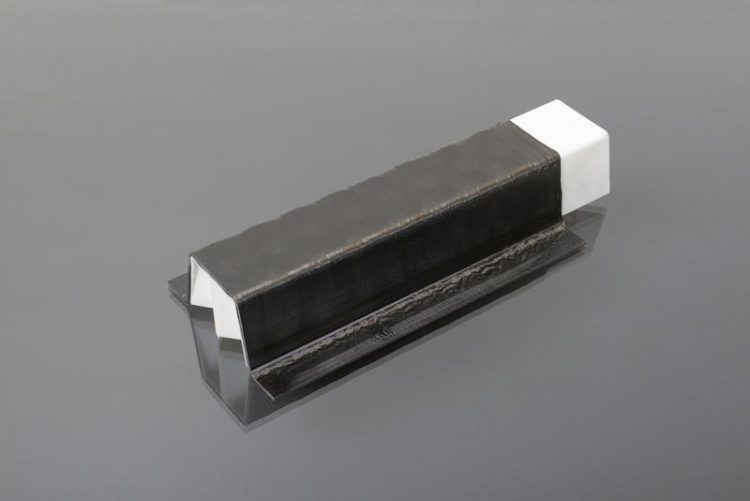
Generativ gefertigtes Demonstratorbauteil, das mit Faserverbundkunststoff gefügt wurde. Bildquelle: Fraunhofer IPT
Der 3D-Druck gewährleistet maximale Flexibilität für Form und Funktion des Bauteils, der Faserverbundkunststoff sorgt für die entsprechende Stabilität, auch unter hoher Belastung. Das Fraunhofer-Institut für Produktionstechnologie IPT aus Aachen untersucht mit seinen Verbundpartnern das kombinierte Herstellungsverfahren jetzt im BMBF-geförderten Forschungsprojekt »LightFlex« und stellt erste Ergebnisse auf der Fachmesse JEC vom 8. bis 10. März 2016 in Paris dem Fachpublikum vor.
Spritzgussbauteile aus Kunststoff, die zur Verstärkung mit Faserverbundkunststoffen kombiniert werden, haben einen großen Nachteil: Sie lassen sich nur schlecht an individuelle Wünsche oder Bedürfnisse anpassen.
Da teure und unflexible Spritzgießwerkzeuge zum Einsatz kommen, ist die Fertigung in der Regel nur in Großserien erschwinglich. Auch spezielle Funktionalitäten oder Änderungen in der Bauteilentwicklung lassen sich nur durch aufwändige Nachbearbeitungsschritte einbringen. Die Herstellung von Kleinserien oder gar Prototypen scheitert deshalb an den hohen Kosten.
Das Fraunhofer IPT und seine Partner im Projekt »LightFlex« planen daher nun, für solche Anwendungsfälle die Spritzgusskomponente durch eine generativ gefertigte zu ersetzen: Durch den 3D-Druck lassen sich die Bauteile nahezu beliebig individualisieren und mit den gewünschten Funktionen versehen, bevor sie mit einem thermoplastischen Faserverbundkunststoff gefügt werden und so die erforderliche Belastbarkeit erreichen.
Um die Belastbarkeit der Bauteile zu optimieren werden für die FVK-Komponente sogenannte Organobleche aus unidirektionalen Halbzeugen verwendet. Anstelle von Standardware mit festgelegten Abmaßen kommen hier jedoch für den individuellen Anwendungsfall zugeschnittene Organobleche zum Einsatz, die auf einer vom Fraunhofer IPT aufgebauten Anlage endkonturnah gefertigt werden. Das minimiert Verschnitt und führt zu deutlichen Einsparungen bei den mit hohem Energieaufwand hergestellten Kohlenstofffasern. Die dazu verwendete Anlage hatte das Fraunhofer IPT bereits im Vorfeld im BMBF-geförderten Projekt »E-Profit« entwickelt.
Die Organobleche kombiniert das Fraunhofer IPT in einem Thermoforming-Prozess mit der 3D-gedruckten Stuktur. Das 3D-gedruckte Bauteil stellte der Projektpartner Wehl Group Sintertechnik GmbH aus Salach bereit.
Insgesamt umfasst das Projekt »LightFlex« die gesamte Prozesskette im Sinne einer vernetzten, adaptiven Produktion – von der Halbzeugherstellung durch das Institut für Kunststoffverarbeitung (IKV) in Industrie und Handwerk an der RWTH Aachen und weitere Partnern bis zur Besäumung mit dem Laserstrahl durch die Arges GmbH.
Auf der internationalen Fachmesse für Verbundwerkstoffe JEC World 2016 in Paris stellen die Partner die Fertigungsanlage sowie ein erstes Demonstationsbauteil, das mit der neuen Verfahrenskombination gefertigt wurde, den Messebesuchern vor.
Partner im Projekt »LightFlex – Photonische Prozesskette zur flexiblen, generativen, automatisierten und wirtschaftlichen Herstellung individuell angepasster hybrider Leichtbauteile aus thermoplastischem Faserverbundkunststoff«
– Adam Opel AG, Rüsselsheim
– AFPT GmbH, Dörth
– Arges GmbH, Wackersdorf
– Breyer GmbH Maschinenfabrik, Singen
– F.A. Kümpers GmbH & Co. KG, Rheine
– Fraunhofer-Institut für Produktionstechnologie IPT, Aachen
– Institut für Kunststoffverarbeitung (IKV) in Industrie und Handwerk an der RWTH Aachen
– KUKA Industries, Reis GmbH & Co. KG Maschinenfabrik, Geschäftsbereich Reis Extrusion, Merzenich
– Pixargus GmbH, Würselen
– Wehl Group Sintertechnik GmbH, Salach
Dieses Projekt wird mit Mitteln des Bundesministeriums für Bildung und Forschung
unter dem Förderkennzeichen 03XP0013 gefördert. Die Projektpartner danken dem BMBF für die Unterstützung.
Kontakt
Dipl.-Ing. Dipl.-Wirt. Ing. Henning Janssen
Fraunhofer-Institut für Produktionstechnologie IPT
Steinbachstraße 17
52074 Aachen
Telefon +49 241 8904-261
henning.janssen@ipt.fraunhofer.de
www.ipt.fraunhofer.de
Diese Pressemitteilung und ein druckfähiges Foto finden Sie auch im Internet unter
www.ipt.fraunhofer.de/de/presse/Pressemitteilungen/20160304lightflexjec.html
Media Contact
Alle Nachrichten aus der Kategorie: Messenachrichten
Neueste Beiträge

Selen-Proteine …
Neuer Ansatzpunkt für die Krebsforschung. Eine aktuelle Studie der Uni Würzburg zeigt, wie ein wichtiges Enzym in unserem Körper bei der Produktion von Selen-Proteinen unterstützt – für die Behandlung von…

Pendler-Bike der Zukunft
– h_da präsentiert fahrbereiten Prototyp des „Darmstadt Vehicle“. Das „Darmstadt Vehicle“, kurz DaVe, ist ein neuartiges Allwetter-Fahrzeug für Pendelnde. Es ist als schnelle und komfortable Alternative zum Auto gedacht, soll…

Neuartige Methode zur Tumorbekämpfung
Carl-Zeiss-Stiftung fördert Projekt der Hochschule Aalen mit einer Million Euro. Die bisherige Krebstherapie effizienter gestalten bei deutlicher Reduzierung der Nebenwirkungen auf gesundes Gewebe – dies ist das Ziel eines Projekts…