Hoch belastbar, weniger Verschnitt
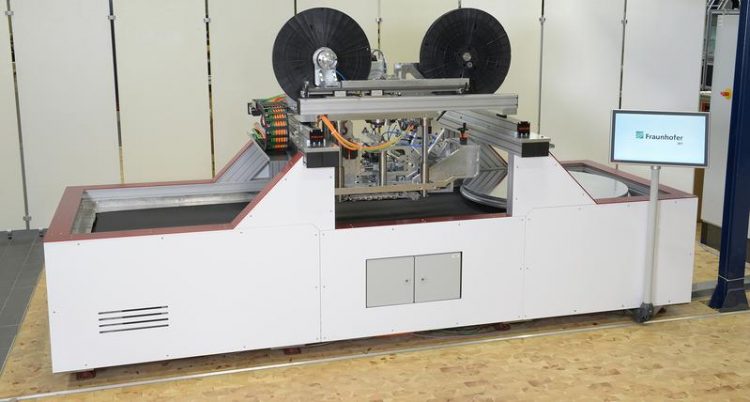
Stand-Alone-System zur automatisierten Herstellung individuell angepasster Organobleche Bildquelle: Fraunhofer IPT
Bei der Herstellung belastungsfähiger Bauteile aus Organoblechen aus Faserverbundwerkstoffen, beispielsweise für den Automobil-, Flugzeug- und Maschinenbau, fällt heute oft ein hoher Anteil an Verschnitt an.
Um hier wertvolle Ressourcen zu sparen, hat das Fraunhofer-Institut für Produktionstechnologie IPT im Forschungsprojekt »E-Profit« gemeinsam mit Partnern eine neue, automatisierte Produktionsanlage entwickelt: Damit lassen sich belastungsoptimierte Organobleche mit weniger Verschnitt herstellen. Vom 22. bis 24. September 2015 zeigen die Aachener Ingenieure die neue Anlage erstmals vollständig aufgebaut auf der Fachmesse Composites Europe.
Organobleche sind Kunststoff-Halbzeuge aus Fasergeweben, die in eine thermoplastische Kunststoffmatrix eingebettet sind. Sie lassen sich durch Erwärmung leicht umformen und gegenüber vielen herkömmlichen Leichtbauwerkstoffen deutlich schneller, ressourcenschonender und energiesparender verarbeiten – bei gleichen oder sogar besseren technischen Bauteileigenschaften. Ein automatisiertes System für die Herstellung belastungs- und verschnittoptimierter Organobleche aus thermoplastischen Tapes war jedoch bisher am Markt nicht erhältlich.
Mit der neuen Anlage aus dem Projekt »E-Profit« können nun sowohl Kohlenstoff- als auch Glasfasertapes mit verschiedenen Matrixmaterialien kombiniert werden. Die Laminate lassen sich durch beliebig einstellbare Faserorientierungen genau an den jeweiligen Anwendungsfall und die gewünschte Belastbarkeit anpassen. Damit gelingt erstmals eine vollständig automatisierte Herstellung belastungs- und verschnittoptimierter Organobleche einschließlich Umformung, Funktionalisierung und Besäumung.
Die sichere und robuste Anlage, die das Fraunhofer IPT gemeinsam mit seinen Projektpartnern entwickelt hat, nutzt Infrarotstrahler als Wärmequelle zum Verschweißen der einzelnen Lagen und kommt ohne Zusatzausrüstung wie Roboter oder Umhausungen aus.
Sie arbeitet bereits heute mit Ablagegeschwindigkeiten bis zu 1m/s und kann Organobleche mit einer Gesamtbreite von derzeit maximal 1 m herstellen. Da die Konsolidierung schon im Herstellungsprozess inbegriffen ist, entfällt außerdem dieser nachgelagerte Prozessschritt. Durch ihre variable, flächige Konsolidierstrecke eignet sich die Anlage damit für eine große Vielfalt an Einsatzfeldern.
Die neue Anlage, die nun erstmals vollständig aufgebaut auf der Sonderfläche »Industry meets Science« der Composites Europe der Öffentlichkeit präsentiert wird, wurde im Rahmen des Forschungsprojekts »E-Profit – Energieeffiziente Produktion funktionsintegrierter thermoplastischer Faserverbundbauteile« entwickelt.
Das Projekt wurde mit Mitteln des Bundesministeriums für Bildung und Forschung (BMBF) im Rahmenkonzept »Forschung für die Produktion von morgen« gefördert und vom Projektträger Karlsruhe (PTKA) betreut.
Tägliche Vorführungen auf der Sonderfläche »Industry meets Science«
Dienstag, 22. September 2015
16.00 – 16.30 Uhr
Mittwoch, 23. September 2015
11.00 – 11.30 Uhr
Donnerstag, 24. September 2015
12.00 – 12.30 Uhr
Kontakt
Dr.-Ing. Michael Emonts
Fraunhofer-Institut für Produktionstechnologie IPT
Steinbachstraße 17
52074 Aachen
Telefon +49 241 8904-150
michael.emonts@ipt.fraunhofer.de
www.ipt.fraunhofer.de
Weitere Informationen:
http://www.ipt.fraunhofer.de/de/presse/Pressemitteilungen/20150914bvo.html
Media Contact
Alle Nachrichten aus der Kategorie: Messenachrichten
Neueste Beiträge

Selen-Proteine …
Neuer Ansatzpunkt für die Krebsforschung. Eine aktuelle Studie der Uni Würzburg zeigt, wie ein wichtiges Enzym in unserem Körper bei der Produktion von Selen-Proteinen unterstützt – für die Behandlung von…

Pendler-Bike der Zukunft
– h_da präsentiert fahrbereiten Prototyp des „Darmstadt Vehicle“. Das „Darmstadt Vehicle“, kurz DaVe, ist ein neuartiges Allwetter-Fahrzeug für Pendelnde. Es ist als schnelle und komfortable Alternative zum Auto gedacht, soll…

Neuartige Methode zur Tumorbekämpfung
Carl-Zeiss-Stiftung fördert Projekt der Hochschule Aalen mit einer Million Euro. Die bisherige Krebstherapie effizienter gestalten bei deutlicher Reduzierung der Nebenwirkungen auf gesundes Gewebe – dies ist das Ziel eines Projekts…