Take five: Aachener Laser-Projekte auf der EuroBLECH 2018
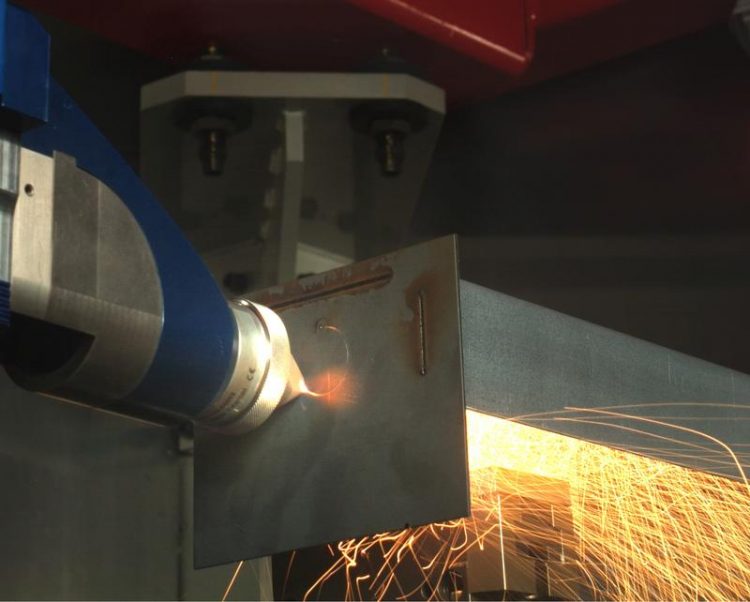
MultiPROmobil ein multifunktionaler Laser-Bearbeitungskopf, der innovative Blechbaugruppen durch integriertes Schneiden, Schweißen und Generieren von additiven Strukturen ermöglicht. © Fraunhofer ILT, Aachen
Für alle fünf Verfahren gibt es einen gemeinsamen Nenner: Sie stehen für verschiedene Ansätze agiler, lasergestützter Fertigung, die den Spagat zwischen Flexibilität und Produktivität schaffen. Gefragt ist dieser Spagat besonders beim hybriden Leichtbau und der Elektromobilität, zwei wesentliche Trends in der Blechbearbeitung.
»Die Lasertechnik ist im Zusammenspiel mit der Digitalisierung eine prädestinierte Lösung, um in volatilen Märkten ständig schwankende und nicht mehr vorhersagbare Losgrößen wirtschaftlich produzieren zu können«, erklärt Dr. Dirk Petring, Gruppenleiter Makrofügen und Schneiden am Fraunhofer ILT.
Cleveres Zusammenspiel von Roboter und Laser-Bearbeitungskopf
Zu diesem Anspruch passt das Leitmarkt-Projekt MultiPROmobil: Das NRW-geförderte Vorhaben startet im Oktober diesen Jahres und wird vom Fraunhofer ILT koordiniert. Ein Roboter und ein multifunktionaler Laser-Bearbeitungskopf sollen durch cleveres Zusammenspiel integriertes Schneiden, Schweißen und das Generieren von additiven Strukturen ermöglichen.
Unterstützt werden sollen sie von einem digitalen Zwilling sowie intelligenter Auslegungs- und Simulationssoftware. Die Aachener und ihre Industriepartner wollen mit MultiPROmobil den zeitlichen Aufwand für die Inbetriebnahme um 30 Prozent und Stückzahlkosten sowie Ressourcenverbrauch um mindestens 20 Prozent senken.
»In einer nachfolgenden Ausbaustufe soll eine Fertigungsanlage mit mehreren Robotern entstehen, in der jeder einzelne Roboter alle drei Fertigungsdisziplinen beherrscht«, blickt Dr. Petring in die Zukunft. »Damit lassen sich Prozessketten für die Herstellung von Blechbaugruppen gerade mit Blick auf die schrittweise Einführung der E-Mobilität sehr flexibel und skalierbar gestalten.«
Aktuell arbeiten die Projektteilnehmer daran, den Kombikopf so weiterzuentwickeln, dass er ohne Optik- und Düsenwechsel zwischen Schneiden, Schweißen und nunmehr auch additiven Prozessen beliebig wechseln kann.
Laserstrahl-Hochgeschwindigkeitsschneiden löst Stanzprozess ab
Ein weiteres Highlight der Aachener Wissenschaftler auf der EuroBLECH ist das flexible Hochgeschwindigkeitsschneiden von Blechbändern: Zusammen mit dem Fraunhofer ILT hat Honda in seinem Werk in Yorii (Japan) das bisherige Stanzen von bis zu 1,8 Meter mal 4,0 Meter großen Stahlblechen mit einer Dicke von 0,5 bis 2,3 mm durch einen extrem schnellen Laserschneidprozess ersetzt, der mit einer Geschwindigkeit von bis zu 115 m/min. arbeitet.
Honda erreicht mit dem Laserschneidsystem seit der Einführung im Jahr 2015 eine Ausbringung von 18.700 Karosserieteilen pro Tag. Dr. Petring: »Wir berichten in Hannover über den nächsten Schritt hin zu einem sehr schnellen Schneidprozess für differenziert gewalztes Band mit partiell unterschiedlichen Eigenschaften, den wir aktuell zusammen mit der BILSTEIN GmbH & Co. KG in Hagen realisieren.
Werkzeuglose Fertigung beliebig variierbarer Schnittkonturen und maximale Materialeinsparung im Fertigungsprozess sowie hinsichtlich des späteren Bauteilgewichtes sind ausschlaggebende Argumente. Wir werden nicht nur ein Video zum Prozess zeigen, sondern auch erste mit unserem Verfahren hergestellte Formplatinen.«
Ultrahochfeste Stähle prozesssicher fügen
Um den Leichtbau-Trend zu ultrahochfesten Stählen geht es im Projekt der Arbeitsgemeinschaft industrieller Forschungsvereinigungen (AiF), das von der FOSTA (Forschungsvereinigung Stahlanwendung e.V.) getragen wird: Im Rahmen von FAAM (Kürzel für: Weiterentwicklung, Fügetechnische Absicherung und technische Auslegung von Schweißverbindungen mit martensitischen Chromstählen) entwickelt das Fraunhofer ILT mit seinen Partnern Laserschweißverfahren, die es an unterschiedlichen Bauteilen erprobt. Als Demonstrator dient beispielsweise ein lasergerecht konstruiertes Stoßfängermodul, an dem die Aachener vorführen, wie sich unterschiedliche hoch- und ultrahochfeste Werkstoffe in Hybridbauweise laserschweißen lassen.
Freiformspiegel kreiert passenden Laserstrahl
Die optimale räumliche und zeitliche Einstellung des Temperaturfeldes spielt die Hauptrolle bei den aktuellen Forschungen auf dem Gebiet der Laserwärmebehandlung. In Hannover zeigt das Fraunhofer ILT, wie sich durch Anpassen des Strahlprofils mithilfe eines Freiformspiegels Bereiche und Zonen gezielt und lokal bearbeiten lassen, um so definierte Festigkeitsprofile zu erzeugen. Um die Laserwärmebehandlung prozesssicher und kosteneffizient mit kurzen Taktzeiten zu realisieren, arbeiten die Aachener mit deutlich erhöhten Vorschubgeschwindigkeiten.
Prozesszeit und Kosten für Rohmaterialien gesenkt
Das fünfte Exponat, ein Dachspriegel, erhielt in Chicago im Juni 2018 bei einem JEC-Event den »Future of Composites in Transportation 2018 Innovation Award« für das Bauteil, das im Rahmen des BMBF-Projekts HyBriLight entstand. Als Vorlage kam ein Originalteil eines Fahrzeugs der BMW 7er-Serie zum Einsatz: ein Hybridbauteil mit faserverstärkter Kunststoffstrebe (bisher rein CFK) und metallischen Anbindungselementen zur Karosserie. Als Alternative zum bisher eingesetzten Kleben und Nieten verwenden die Aachener einen laserbasierten Fügeprozess, der Kunststoff und Metall per Formschluss und Adhäsion miteinander verbindet.
Außerdem wurden die Materialkosten durch Nutzung von GFK statt des teureren CFK deutlich reduziert. Letzteres wird jetzt nur noch als festigkeitssteigernde Einlage an den Längsseiten der Strebe verwendet. Mit einem innovativen Laserschneidprozess, der die Bearbeitung des Materialverbundes aus GFK und CFK in einem Arbeitsschritt erlaubt, wird der Dachspriegel abschließend besäumt. Für die Innovation sprechen mehrere Pluspunkte:
Reduzierung der Prozesszeiten im Vergleich zu konventionellen Verfahren um 70 Prozent, Halbierung der Rohstoffkosten und die Integration mehrerer Prozessschritte in einen Prozess. »In Hannover zeigen wir die neue Dachspriegelvariante, an deren Materialmix aus GFK, CFK und Metall die vielseitigen Einsatzmöglichkeiten der Laserbearbeitung zum Fügen und Schneiden von komplex aufgebauten Bauteilen demonstriert werden«, berichtet Dr. Frank Schneider, Senior-Projektmanager in der Gruppe Makrofügen und Schneiden am Fraunhofer ILT.
Anhand von Demonstratoren, Bauteilen und Videos erläutern die Forscher des Fraunhofer ILT auf der EuroBLECH vom 23. bis zum 26. Oktober 2018 in Hannover (Halle 11, Stand A25), den aktuellen Stand der Entwicklung der fünf Projekte.
Dr. rer. nat. Dirk Petring
Gruppe Laserschneiden
Telefon +49 241 8906-210
dirk.petring@ilt.fraunhofer.de
Dr.-Ing. Frank Schneider
Gruppe Laserschneiden
Telefon +49 241 8906-426
frank.schneider@ilt.fraunhofer.de
http://www.ilt.fraunhofer.de
http://www.euroblech.com/2018/deutsch/
Media Contact
Alle Nachrichten aus der Kategorie: Messenachrichten
Neueste Beiträge

Ist der Abrieb von Offshore-Windfarmen schädlich für Miesmuscheln?
Rotorblätter von Offshore-Windparkanlagen unterliegen nach mehrjährigem Betrieb unter rauen Wetterbedingungen einer Degradation und Oberflächenerosion, was zu erheblichen Partikelemissionen in die Umwelt führt. Ein Forschungsteam unter Leitung des Alfred-Wegener-Instituts hat jetzt…

Per Tierwohl-Tracker auf der Spur von Krankheiten und Katastrophen
DBU-Förderung für Münchner Startup Talos… Aus dem Verhalten der Tiere können Menschen vieles lernen – um diese Daten optimal auslesen zu können, hat das Münchner Startup Talos GmbH wenige Zentimeter…

Mit Wearables die Gesundheit immer im Blick
Wearables wie Smartwatches oder Sensorringe sind bereits fester Bestandteil unseres Alltags und beliebte Geschenke zu Weihnachten. Sie tracken unseren Puls, unsere Schrittzahl oder auch unseren Schlafrhythmus. Auf welche Weise können…